Top 10 Welding Techniques Every Welder Should Know
Insights into the top 10 welding techniques that every professional welder should know
7/14/20243 min read
Top 10 Welding Techniques Every Welder Should Know
Welcome to the JM Welding Repair Solutions Inc. blog! In this post, we’re sharing expert insights into the top 10 welding techniques that every professional welder should know. Whether you're a seasoned welder or just starting, understanding these essential methods will help you achieve optimal results in your projects. Read on to discover the techniques that JM Welding Repair Solutions Inc. employs to deliver exceptional welding services in Hayward, CA.
1. Shielded Metal Arc Welding (SMAW)
Overview
Shielded Metal Arc Welding, commonly known as stick welding, is one of the most widely used welding techniques. It involves using a consumable electrode coated in flux to lay the weld. The electric current forms an arc between the electrode and the metals to be joined.
Applications
Construction
Repair and maintenance
Industrial fabrication
Benefits
Versatility in different environments
Low cost of equipment
Suitable for thick materials
2. Gas Metal Arc Welding (GMAW/MIG)
Overview
Gas Metal Arc Welding (GMAW), or Metal Inert Gas (MIG) welding, uses a continuously fed consumable wire electrode and a shielding gas to protect the weld pool from contamination.
Applications
Automotive industry
Manufacturing
Structural welding
Benefits
High welding speed
Minimal post-weld cleaning
Easy to learn and use
3. Gas Tungsten Arc Welding (GTAW/TIG)
Overview
Gas Tungsten Arc Welding (GTAW), also known as Tungsten Inert Gas (TIG) welding, utilizes a non-consumable tungsten electrode to produce the weld. A separate filler material is often used.
Applications
Aerospace
Piping systems
Stainless steel and non-ferrous metals
Benefits
High precision and control
Produces clean, high-quality welds
Suitable for thin materials
4. Flux-Cored Arc Welding (FCAW)
Overview
Flux-Cored Arc Welding (FCAW) is similar to MIG welding but uses a special tubular wire filled with flux. It can be used with or without a shielding gas.
Applications
Heavy equipment repair
Construction
Shipbuilding
Benefits
High deposition rate
Works well outdoors
Effective on dirty or rusty materials
5. Submerged Arc Welding (SAW)
Overview
Submerged Arc Welding (SAW) involves forming an arc between a continuously fed electrode and the workpiece, with the weld area submerged under a blanket of granular flux.
Applications
Pressure vessel fabrication
Large structural components
Pipelines
Benefits
High productivity
Deep weld penetration
Minimal fumes and arc light
6. Oxy-Acetylene Welding (OAW)
Overview
Oxy-Acetylene Welding (OAW), or gas welding, uses a flame produced by burning a mixture of oxygen and acetylene to melt the workpieces and filler material.
Applications
Automotive repair
Metal art and sculpture
Thin sheet metal
Benefits
Portability
No need for electricity
Versatile for cutting and welding
7. Plasma Arc Welding (PAW)
Overview
Plasma Arc Welding (PAW) uses a plasma torch to generate a highly focused and stable arc, allowing for precise welding.
Applications
Aerospace components
Medical devices
Stainless steel fabrication
Benefits
High precision and control
Deep penetration welds
Suitable for automated welding systems
8. Electron Beam Welding (EBW)
Overview
Electron Beam Welding (EBW) uses a beam of high-velocity electrons to join materials. This process is performed in a vacuum to prevent the electron beam from scattering.
Applications
Aerospace and defense
Nuclear components
High-precision manufacturing
Benefits
Extremely high penetration
Minimal thermal distortion
Suitable for thick materials
9. Laser Beam Welding (LBW)
Overview
Laser Beam Welding (LBW) employs a laser to melt the materials being joined. This method is known for its precision and is used for high-speed, high-quality welds.
Applications
Electronics
Medical devices
Automotive industry
Benefits
High precision and control
Low heat input
Suitable for thin and delicate materials
10. Resistance Spot Welding (RSW)
Overview
Resistance Spot Welding (RSW) joins metals by applying pressure and passing an electric current through the workpieces. The heat generated by the resistance to the electric current melts the metal at the joint.
Applications
Automotive assembly
Sheet metal fabrication
Appliances
Benefits
Fast and efficient
Minimal distortion
Suitable for automated processes
Conclusion
Understanding these top 10 welding techniques is essential for any professional welder looking to excel in their field. At JM Welding Repair Solutions Inc., we utilize these methods to ensure the highest quality in all our welding projects. Whether you need structural welding, equipment repair, or custom fabrication, our team in Hayward, CA, is equipped with the knowledge and skills to deliver outstanding results.
JM Welding Repair Solutions Inc. is your trusted partner for quality welding repair services. With a commitment to excellence and innovation, we're dedicated to helping you achieve superior results in your repair projects. Connect with us today to experience the difference of working with a true welding repair expert.
Address
2382 American Avenue Hayward, CA 94545
Hours
Monday - Friday 8:00AM -5:00PM Saturday - Sunday Closed
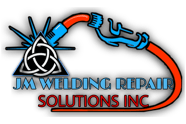

Payment Accepted
Visa, Mastercard, American Xpress, Disocover, Cash, Check, Venmo, Zelle
About Us
We collaborate with reputable suppliers, ensuring access to top-of-the-line materials